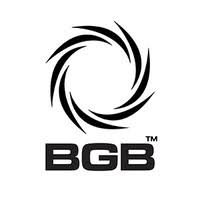
Advanced manufacturing in action: Freudenberg Sealing Technologies accelerates its tool-making processes.
Challenges
- The understanding of the types of Milling tools was new to the team
- Connecting with a tool supplier that could help them understand the best tools to use with these new techniques they must learn.
Solutions
- Design team to be trained in the use of Turn-Mill techniques using Autodesk FeatureCAM.
- This training would involve Turning, Milling and Turn-Mill techniques.
Benefits
- The impact of this training and services meant that FST is closer to an automated process, which eliminates errors in machining.
Contact us
Please submit your enquiry here and a member of our team will get in touch.
Alternatively call 0345 370 1444