Sovelia Core takes digital transformation to new heights for access equipment manufacturer, Planet Platforms
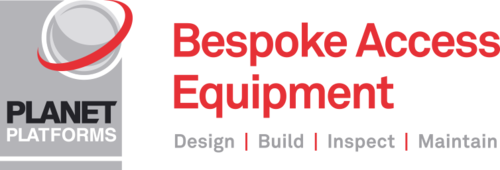
Planet Platforms is at the forefront of the Safe Access Equipment manufacturing sector. Innovators in the design and manufacture of bespoke modular safe access equipment, the company supports working at height safety measures in locations that are nearly always characterised by risk. Planet Platforms has over 40 years of working at height experience, helping companies such as BAE Systems, Rolls-Royce and the Bristow Group.
“With Sovelia Core, Symetri proved to us that we could work differently, which meant working better. The solution has become like an additional member of staff, making workflows smoother, ensuring quality data, minimising errors, and saving time. When you put those benefits together, plus numerous others, the most significant transformation we’ve achieved is that we complete more projects every month. The software itself is the best thing we ever did, lifting the whole team’s competencies (and confidence in getting it right first time every time) to new heights.
Symetri guided us every step on the way
to achieving fully joined-up product lifecycle management”.
- Carl Geldard, CAD Manager, Planet Platforms
In addition to aircraft maintenance and helicopter access platforms, the company provides solutions for sectors including rail (train access), vehicle fleet maintenance in distribution and logistics, and manufacturing (from moving vehicle production lines to food processing plants).
The aim of all the company’s solutions is to eliminate the risk of falling associated with using unsuitable access equipment. Benchmarking its products against relevant directives is a priority that, as a manufacturer, Planet Platforms holds as the prime focus in all its processes. From design through to production and testing, diligent assessments are carried out to ensure that its products meet high health, safety and environmental requirements.
The challenge: Embrace digital benefits to truly connect design with production — effortlessly, rapidly, and collaboratively
Making the leap into smart manufacturing
Carl Geldard is Planet Platform’s CAD Manager. He has a deep understanding of how labour-intensive the process of translating CAD drawings into production-ready specifications can be from his own experience in production. Carl joined the company in 1989 as a welder, working on the shop floor.
When he moved into the design office, Carl worked with Symetri along various stages of updating the drawing office’s technology. Carl’s role was to bring CAD into the company, a journey which started with Mechanical Desktop and eventually progressed to Inventor. The relationship with Symetri goes back almost 20 years.
“We had adhered to certain traditional working methods which had suited us for many years. Designers would create a drawing, pass it through to the shop floor, with accompanying Excel spreadsheets for components and Bills of Material, and the shop floor would make sense of it all.
I knew what that was like. It was a cumbersome process; duplicate files often led to interpretation errors. This was the way of things. It was part of the skills of the production team to unravel these issues. The team would resolve problems on the fly.
This didn’t seem like a big deal until Symetri advised how much we stood to gain by investigating the discipline of product lifecycle management, a lean approach to manufacturing that could propel our processes into the paperless world of smart manufacturing. This intrigued us”.
Creating workflows that flow
Planet Platform’s drawing office had shelves of paper-based files. Manufacturing team members were always popping into the office to clarify information and requirements. These interactions bonded the teams in a shared commitment to creating quality solutions of the highest order. Such queries also added time to project completion. The delays were avoidable. It was just a matter of finding out how.
“We knew we could do more”, says Carl. “We knew that somehow these interactions could be automated and the workflow could just flow. We asked Symetri to recommend how this could be done”.
The solution: Sovelia Core — turbo-charged innovation
From manual to digital
Following an end-to-end evaluation of Planet Platform’s design-to-manufacture process, the Symetri team recommended that, while strong connected and interactive team bonds had served the company well, a digital approach could significantly empower its connections and interactions. With that in place — with a bond created by data rather than problem-sharing — people could engage with each other far more to explore new ideas, sharing visions and insights rather than clarifying interpretations arising from design drawing issues.
For example — returning to the often-encountered problems of interpreting data held on Excel spreadsheets; for each bespoke product, the components would need to be copied from the spreadsheet. Duplications could be rife when this happened, given that components often number in their thousands. Manual checking was traditionally the only way for the Planet Platforms production team to remove them.
Symetri recommended that previous manual processes go digital.
Reliable and trustworthy data
Symetri meets with many customers who are pleasantly surprised when they discover that the entire product lifecycle management solution that PLM delivers can bring significant advantages to companies of any size. Small and Medium Enterprises — the category applicable to Planet Platforms — gain all the same efficiency benefits that large enterprises depend on.
These benefits include workflow automation, reduced errors, and higher-quality data that can be relied on as correct. In other words — they are eliminating risk to the integrity of project schedules.
“Sovelia Core was a revelation for us”, Says Carl. “Based on the irrefutable logic of having all data in one central repository through a data management system we attained the game-changing benefit of one single version of the truth. No more toing and froing to de-dupe the information, with all the time-wasting caused, and no omissions.
Our new PLM system was up and running after the essential data migration phase, which Symetri undertook for us. It was the best thing we ever did”, says Carl.
The outcomes: Everything was fixed all at once — A digital platform | A tighter process | A confident team
“Our design office comprises three people. Planet Platform’s growth was accelerating. Dealing with increased demand wasn’t a problem, but dealing with constant issues from the shop floor relating to information, clarifying it, revisiting it, talking through the design concept, all these interruptions to workflows were impacting our workload”, says Carl.
The workflow benefits
- Finite detail assured
Describing the benefits of the automated processes driven by Sovelia Core, Carls says: “It effectively all starts with the metadata. Sovelia provides rich, high-quality, accurate data that depends on finite detail, which was the area of highest risk in our manual days. For example, Sovelia ensures no missing cells in parts lists by filling out the property cards and prompting action where required. - Processes accelerated
Carl also explains that re-using commonly occurring parts lists is far easier: “You locate components just by pressing a button, not by embarking on a tedious search as previously”. - Notifying the right person at the right time
Sovelia PLM also ensures timely approval processes, ensuring that information is only available to the design office when a project is in design. It then releases information more broadly when the design is ready and only provides visibility to the workshop when those two stages are complete, and production can commence. - The workflows now flow
From the CAD office through to the workshop team, whoever needs to access information can do so anywhere, on any device. “Our teams are more efficient now since they can gain the information they need exactly when they need it, on a smartphone or a tablet. The great change here has been that they all feel more efficient.
I’ve always believed that a happy team makes for happy customers. That’s why everyone here embraced Sovelia Core the minute they saw what it could do”.
Embracing modern manufacturing
“In all the time I’ve worked with Symetri, I’ve found the team — everyone — highly personable”, says Carl. “They’ve supported Planet Platforms as we’ve grown, and they haven’t encountered a problem they couldn’t solve for us. We have weekly meetings with them where they highlight issues that we should be aware of. Then they fix them.
Our relationship is also about far more than keeping things ticking over. Symetri is our trusted advisor. They keep us abreast of technology developments, always considering the next step in our digital transformation journey. They care about our business and keep our pace of innovation in line with the expectations our customers have of us as a leader in our field. Symetri is core to enabling Planet Platforms to embrace modern manufacturing”.
Learn more about what Sovelia Core can do for your process efficiencies, optimising smarter data management and easier collaboration across your company by filing in the form.
Challenges
- Embrace digital benefits to connect design with production, effortlessly, rapidly and collaboratively
- Avoid delays to project completion time
- Leaving traditional working methods to new drawing technologies
- Eliminate the duplications of files and interpretation errors
- Moving away from paper-based files and taking a digital approach.
Solutions
- Sovelia Core product information management system was optimised to suit Planet Platform requirements
- Using PLM to create workflow automation to reduce errors and produce high-quality data
- Moved away from manual processes to a digital approach
Benefits
- Sovelia Core drives accurate automated processes
- Processes are now accelerated at the touch of a button rather than previously doing a tedious search
- Timely approval process - notifications to the right person at the right time
- Access to information anytime, anywhere on any device
Related Cases
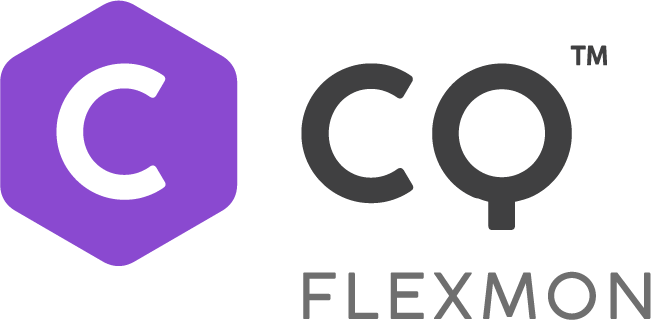
NO MORE SPIRALLING SOFTWARE COSTS - JUST DATA-DRIVEN PRECISION WITH CQFLEXMON
MEET "THE" ARCHITECTS This acclaimed design practice is known for delivering high-quality work across architecture, master planning, and interior design. With particular strengths in the workplace, lifestyle and leisure, and residential sectors, t... Learn more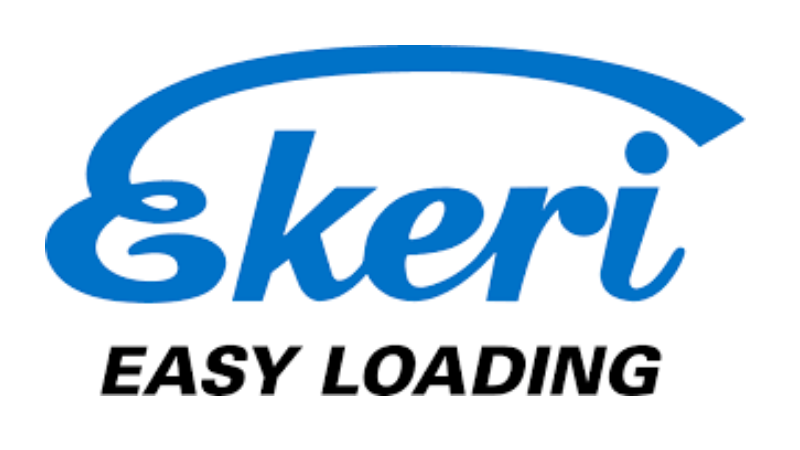