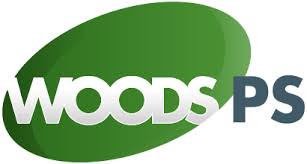
Stepnell’s BIM approach; ‘no stone unturned’ for University of Worcester
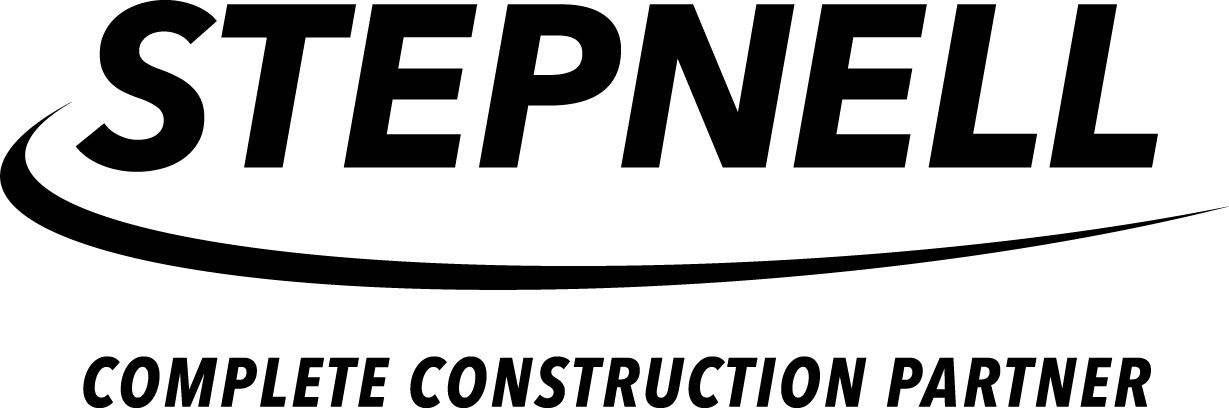
The digital journey from construction through to facilities management.
This is a story of using multiple technologies on a refurbishment and extension project— gaining maximum insight and value from a Revit 3D model, streamlining workflows, formatting data for direct input from the design models into a Computer Aided Facilities Management (CAFM) system, through to the use of point cloud technology to assist subcontractors, and monitor site progress every step of the way.
Meet Stepnell
Stepnell is a complete construction partner, with end-to-end project lifecycle expertise. The company’s overriding goal is to ensure that their clients realise their visions. Stepnell’s depth of expertise and holistic approach gives clients the confidence that every aspect of their project will be efficiently executed, to the highest standards, in a collaborative manner.
With over 150 years’ heritage in the industry, and an experienced, commercially responsible management team setting direction, Stepnell is a financially resilient business, with over £58 million in net assets.
Stepnell serve a broad spectrum of private and public sector clients. They combine the focus and accessibility of a regional contractor, with a depth of technical competency, professional capability and national reach, usually associated with far larger construction companies.
The project overview: Elizabeth Garrett Anderson building - A showcase project laying the ground rules for the future
Stepnell was successful in its tender for a project from University of Worcester that involved transforming the former Worcester News building—a large two and three storey 1965 building - into a first-class centre for the education of health professionals.
The building has been named by the University as the Elizabeth Garrett Anderson building, in honour of the first woman in Britain to qualify as a physician and surgeon.
The project was partly refurbishment and partly a new build; stripping back to shell and core and then building an extension. The process of capturing the existing structure and tying it into the new build required diligent planning, particularly within the context of generating point cloud information.
Furthermore, the University team specified that the use of a robust Computer Aided Facilities Management (CAFM) system will be used which requires information to be accurately populated from the maintainable assets in the building. This latter requirement being a particular challenge when it came to aligning the data against strict parameters between the Revit model and the CAFM system. There were more challenges besides, which presented Stepnell with the opportunity to create an approach to projects of such complexity, which could then be used as a template for projects in the future.
An entire multi-disciplinary team of specialist technology providers came together to ensure adherence to use Building Information Modelling (BIM) guidelines, whilst adapting to the unique requirements the University expressed for its CAFM system.
Rising to the challenge
STAGE 1: Preparing to succeed
- Establishing the BIM level 2 framework
The University of Worcester had a clear vision of wanting to use BIM on the project. They were intent on the use of Revit 3D collaborative models as well as the idea of ensuring that all data relevant to facilities management post-handover could pass from the Revit model through to the CAFM system, Archibus. This system was not yet installed.
During the tender stage, Stepnell had included Symetri as its named BIM partner for information management, a role which quickly expanded. Before they could create their specific clarified requirements for Stepnell, the University’s Service Development Manager for Estates and Facilities reached out to Symetri both for guidance on the requisite detail and documentation for the BIM Level 2 project and for setting up the facilities management system. These two foundational strands of project preparation got underway in parallel.
Symetri guided the University team through each of the essential BIM requirements, protocols and associated project planning, and created key documents such as the BIM Execution Plan (BEP). They also demonstrated how workflows would be integrated between the construction phase (and before) to facilities management (and beyond).
- Simplifying the data focus
The University team appointed Service Works Global (‘SWG’—part of the same group as Symetri) under a separate service to the BIM support services. SWG are specialists in computer aided facilities management, who guided the setup of Archibus to meet the precise requirements of the University around pertinent data and asset information.
Meanwhile, attention had to be paid both to the nature of the data, and the way it was presented to match the file data coding with Archibus, so that the parameters were shared; to include information such as the building code, warranty details, classification codes, and serial numbers.
It is often the norm to use Construction Operations Building Information Exchange (COBie) data for these purposes, but the University had a clear requirement on the precise fields of information they needed for the maintenance of their CAFM system, so it was decided to structure the data in a bespoke fashion. Data available in the 3D model is also not easy to digest for people who are not necessarily 3D-capable. Simplicity is the most direct route to understanding. For example, asset manuals can now be easily accessed by having the URL embedded in both the Revit file and Archibus.
Symetri and SWG formatted the data fields in collaboration with one another, and guided population of the information from the design teams and suppliers directly into the database. The specific goal of this collaboration was to set up a flow of data—between Archibus and the project models—so that changes could be made in the model authoring software and then be easily exported, issued to the university and imported into the CAFM system (Archibus). To ensure that the information was correct before pushing to the university, there were regular data-drop dates established which required a general ‘health-check’ on the models from Symetri. To ensure reliability and correct assignment of the data, and to check the quality of information within the model, Symetri used Solibri.
We’re ready
“At this early stage we knew that every aspect of both the BIM parameters for the project and the smart use of data both within and beyond it had been addressed” says Charlotte Brogan, Technical Manager at Stepnell.
“The University was up to speed on how to adhere to BIM protocols and were reassured that the team that we had around us in specialist support roles, were giving everybody a lot of confidence”.
STAGE 2: On-site—making the connections between physical and digital
With the CAFM system in place and the BIM direction of travel defined, documents prepared, and all involved parties brought up to speed, it was time to address how what happened on site, would not sit alone as a physical exercise, while information capture and data foundations for facilities management sat in a different digital world.
- Gaining visibility of the frame
LA laser scan was required to show the frame after the strip-out. The intention then was to bring the point cloud data together with the 3D models. This was an essential stage from the point of view of MEP and structural contractors. For example, the roof cladding providers needed to see how the roof looked to assist their process of building the roof cladding (a gold copper shingle) offsite. The point cloud was also essential for clash detection purposes.
The next specialist company came on to the team at this point. Symetri introduced Stepnell to 1st Horizons, experts in, among other things, 3D laser scanning. An invaluable lesson was learned at this stage around the specifics of point cloud.
A straightforward scan will scan all the elements in its path. Even when these are subsequently meshed, they do not convert into the ‘solid’ elements that Revit requires. The way round this is to commission a ‘Scan To BIM’ which produces a 3D geometric shape compatible with Revit.
- Seeing the site progress 360° image capture
Looking at what’s going on onsite to make sure the model reflects reality has traditionally involved precisely that—going onsite and looking. This can be a time-consuming exercise requiring using a camera (or smartphone camera), uploading the shots, attaching them and sending them.
Via a hard-hat mounted camera, Oculo builds a 3D walk environment by taking thousands of continuous shots such that the end result closely resembles video footage and can be fully manipulated on-screen (zoom in and out, rotate etc). A key function of Oculo is the ability to import the project clash detected federated model directly into Oculo, which can be used to compare the scans of the physical as-constructed state on site against the design intent models.
“Oculo has really sped up so many tasks that were previously so painstakingly slow”, says Charlotte. “As-built checks are now easy and also deeply detailed, allowing us to compare what is happening on the site directly to the model”. Charlotte also says that changes can now be made to the design and not onsite, the far more costly alternative.
The outcomes
The Elizabeth Garrett Anderson project got underway on 6th June 2021 and is on track for completion in December 2022.
More than just the project completion, it has been a valuable exercise in educating all parties in best practice in digital and physical, and linking the two together:
- University of Worcester intends to use its new BIM standards (such as the EIR and the AIR), to define all projects going forward.
- University of Worcester now has an up and running CAFM system.
- Data is now formatted for feeding into Archibus from the model.
- Clarity, collaboration, and contentment—a winning combination.
About Service Works Global
Service Works Global (SWG) is a leading international provider of facilities, property and workplace management software with offices in the UK, Sweden, Canada, Australia, and the Middle East. SWG is a wholly owned subsidiary of Addnode Group, listed on Nasdaq Stockholm.
Established in 1994, SWG is a Microsoft Gold Partner, certified with ISO 9001 for quality management and ISO 27001 for information security management, and has a wealth of expertise in computer-aided facilities management (CAFM), public-private partnership (PPP), and building information modelling (BIM) software.
We invest substantial resources into product research and development to ensure functionally rich solutions that meet the needs of an evolving profession. Some of the clients that we support include Honeywell, Mitie, BNP Paribas Real Estate, Melbourne Cricket Ground, Cardiff University and NHS Trusts across the UK.
For more information, visit www.swg.com.
Related Cases
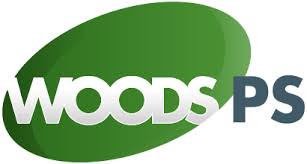
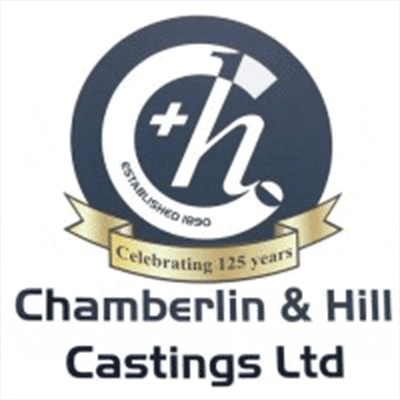
Chamberlin & Hill reduced the number of administrative workflows and mistakes made using Fusion Manage
Meet Chamberlin & Hill Chamberlin & Hill is the light castings division of Chamberlin plc, specialising in castings up to approximately 40kg, often with complex shapes and fine tolerances requiring highly skilled manufacturing methods–predominantl... Learn more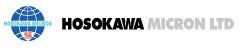