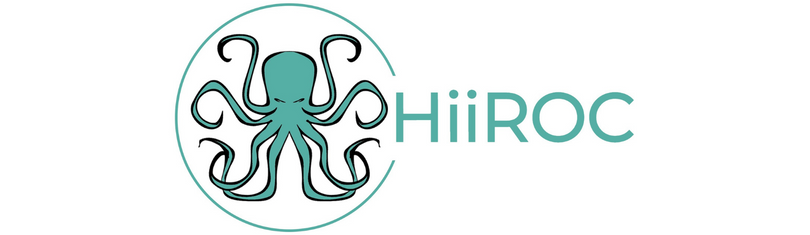
Symetri’s Autodesk Fusion 360 training consolidates skills for manufacturing R&D support at the University of Aberdeen’s engineering workshop
Challenges
-
Reduce wastage resulting from the hand-finishing rendered necessary by using the old version of post-processor software.
-
Minimise client rejection rate and associated costs of re-supplying replacement products.
-
Improve quality.
-
Accelerate lead times.
Solutions
-
Post-processor upgrade to enable automation of the tapping cycle.
-
Align post-processor with machine kinematics.
-
Hardware addition of Floating Tap Collet to eliminate manual inaccuracies.
Benefits
-
Fully automated tapping cycle ensuring greater accuracy.
-
Significant reduction in rejected output at client’s QA inspections.
-
Improved quality.
-
Higher levels of client satisfaction, now leading to new business opportunities.